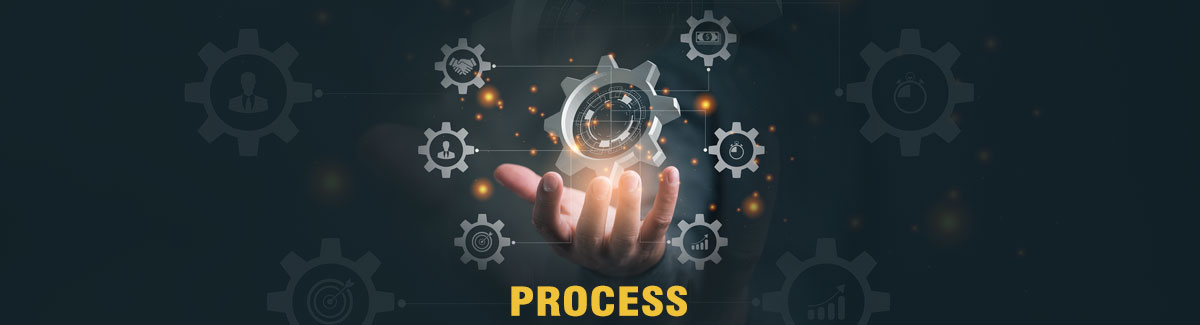
Manufacturing
Process
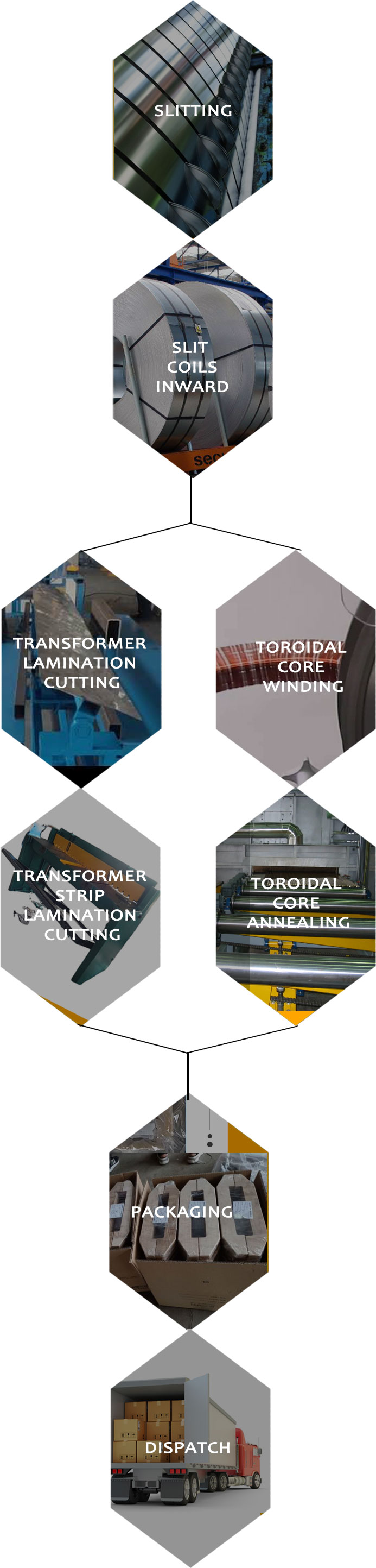
SLITTING
Consisting of 2 Slitting Lines with high quality cutting blades for high quality precise slitting with minimum burr levels to obtain desired width of coils for manufacturing Transformer Lamination and Toroidal Cores.
SLIT COILS INWARD
Once the slitting process is completed these coils are taken inward in the ERP System and placed in the coil storage facility or store to maintain a perfect stock.
TOROIDAL CORE WINDING
These slitted coils of the specific slit height are then processed on the automatic or conventional core winding machines for making CRGO round and rectangular cores as per customer specifications.
TOROIDAL CORE ANNEALING
These cores are then stress annealed up to 800 Degree Celsius to attain the desired electrical losses as per customer specification and requirements.
TRANSFORMER LAMINATION CUTTING
Once the desired width coil is obtained after the slitting process the next step is cutting where these coils are cut at specific length at 45- or 90-degree in Conventional & Step Lap (Horizontal & Vertical) design and various operations like V-notching at 45-degree angle and holing are performed as per the core design requirement by the customer.
TRANSFORMER STRIP LAMINATION CUTTING
As we strictly adhere to lean management, we make sure that the balance waste of these high quality CRGO lamination is further used for cutting and obtaining strip lamination of desired size and design.
PACKAGING
The packaging stage is the most delicate and crucial process as these materials are overly sensitive in nature and high level of utmost precision must be taken while packing these finished CRGO products. Wooden block pallets are placed beneath and these CRGO Finished Goods are wrapped in transparent stretch wrap. In case of Transformer Laminations, the stacks are packed in such a manner that it is convenient and easy for the customer’s assembly team to assemble the core.
DISPATCH
We carry out dispatch by Road, Sea & Air as per the destination and feasibility.